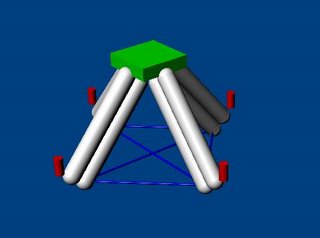
There are so many ideas and trade offs that it's hard to pin down a design. My current best guess for a vehicle is shown on the left. Its a lox ethanol vehicle with 4 250 lb thrust chambers. I'll try to describe it. The gray cylinders are aluminum irrigation tubing with hemisphere end caps. The red cylinders are the 4 motors. The green box is the payload and avionics. The blue lines are either spectra or kevlar lashings. Landing gear is not shown, but may be as simple as foam blocks under the tanks with additional shock absorption from give in the lashings. I like this design because I can test the tank and motor systems in a configuration identical to the final vehicle. I can even build up spare tank and motor assemblies. The other leading design candidate is a vehicle using 4 spherical tanks with four motors on the corners. In some ways a 50% scale pixel.
This is the first time I've actually drawn the vehicle in CAD. It has existed in many, many spreadsheets. The spreadsheet that goes with this vehicle can be found in PDF or XLS formats. The rest of this post won't make much sense unless you follow along on the spread sheet.
The top left of the spread sheet has a table of weights. I'm doing this both in Kg and pounds. To do any real physics type math MKS systems are better, but being an American I grew up with pounds and just can't kick the habit. The weights are listed along with the number of them on the vehicle. Several of the weight items are calculated. for instance the weight I assign to each thrust chamber is the peak motor thrust divided by 30. As the tanks have the most mass the tank calculations are more detailed. I use aluminum tubes where I can enter the length diameter and thickness, the spread sheet then calculates the weight and interior volume for a single tank. These numbers end up in the weight table. Finally I use the weight table and propellant mass. (labeled fuel in the spread sheet) to calculate the delta vee (DV) and number of hover seconds.
Some general notes:
- Things labeled fuel really mean propellant. I've used an average fuel and oxidizer combined density of 0.8 gm/cc (At 1 ATM this would actually be about .92)
- I only plan to fill the tanks to 90%.
- The design includes 2 carbon fiber wrapped cylinders and a regulator to provide presurant gas to the point where the tanks are 60% full and then it runs in blow down mode from there on.
- I've hidden a whole bunch of stuff in the "structure" item I hope to not need much structure beyond the tanks.
- I'm assuming that I use aluminum tanks for both LOX and Ethanol, if I get into weight trouble I can build composite Ethanol tanks and probably save 16 Kg
- I have a burst safety factor of 2.3 in the aluminum tanks. If I need more performance I can increase the tank and chamber pressures as the system can be pressurized remotely. The CF cylinders are DOT rated for 2200 psi, with a SF of better than 3 so I can probably get the extra pressureant I need from these. This would imply a remote presurant tank top off.
- As per my communications with the XPC rules people any AST required safety shutoff valves etc.. are counted against the 25 Kg payload.
- I used 25% of Cp for system and injector pressure drop.
- I used 80% of the Cpropep frozen sea level ISP for my target ISP.
Comments are welcome.
3 comments:
Trust me, you don't want to use foam for the landing gear. It was great on our little tiny peroxide vehicles, but big vehicles (let alone biprop one) start depositing molten foam everywhere, for a mess that you will never be rid off.
The simplest and most robust landing gear is to use some big wire rope isolators, but they are very heavy compared to a hydraulic or pneumatic shock.
John Carmack
John,
Thanks for the foam tip.
The problem with a shock type landing gear is that it is only really good at absorbing force in a single direction.
From watching Pixel at XPC it was clear that the drift will never be zero and some method to absorb force from random directions must be found.
Something like helicopter landing skids might be reasonable.
Interesting blog I'll check in often to see how things are going. I think sometime ago on Arocket you were interested in self pressurizing propellants are you giving up on that idea and committing to the LOX/ethanol combo?
Post a Comment